Selektywne topienie laserowe (SLM) to nowoczesna technologia, którą producenci tłumików zaczynają wykorzystywać do produkcji wysokiej jakości produktów. Początkowo opracowana z myślą o przemyśle lotniczym, motoryzacyjnym i medycznym, technologia ta znalazła swoje miejsce także w produkcji tłumików. Proces drukowania tłumika 3D jest zaawansowany technologicznie. Najpierw tworzony jest komputerowy model CAD, który odwzorowuje finalny produkt. Następnie drukarka 3D do metalu rozprowadza cienką warstwę drobnego proszku metalowego, który jest topiony za pomocą lasera, tworząc pierwszą warstwę tłumika. Proces ten jest powtarzany warstwa po warstwie, aż do ukończenia tłumika.
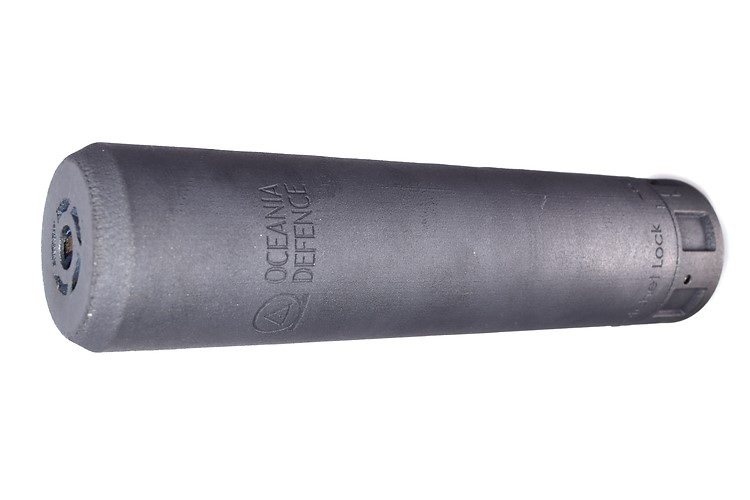
Wydajność i trwałość tłumików drukowanych w 3D
Druk 3D umożliwia tworzenie tłumików o konstrukcjach, które wcześniej były niemożliwe do osiągnięcia. Tradycyjna obróbka ubytkowa nie pozwalała na budowę złożonych struktur, które dzisiaj możemy znaleźć w tłumikach drukowanych w technologii L-PBF (SLM/DMLS). Dzięki tej swobodzie projektowej można wykorzystać więcej przestrzeni wewnątrz tłumika oraz inaczej kierować gazy, co prowadzi do licznych ulepszeń:
- Lepsze tłumienie dźwięku.
- Zmniejszenie rozbłysku.
- Mniejsze ciśnienie zwrotne (w porównaniu do tradycyjnie produkowanych modeli).
Tłumiki, które powstają na drukarce 3D do metalu są również wyjątkowo wytrzymałe. Drobny proszek metalowy i precyzyjny laser tworzą jednorodną strukturę, co eliminuje słabe punkty, które mogą występować w tradycyjnie produkowanych tłumikach.
Wybór stopu: kluczowy element w projektowaniu tłumików
Druk 3D przy użyciu technologii L-PBF (SLM/DMSL) pozwala na użycie materiałów, które są tradycyjnie trudne do obróbki lub drogie w użyciu, takich jak Inconel i tytan. Inconel jest bardzo trwałym metalem, który nie traci swoich właściwości pod wpływem wysokiej temperatury, co czyni go idealnym materiałem na tłumiki. Chociaż jest trudny do obróbki, L-PBF omija te trudności, umożliwiając budowę tłumików w całości z Inconelu, co czyni je wyjątkowo wytrzymałymi. Tytan, dzięki swojej wytrzymałości i lekkości, jest również doskonałym materiałem na tłumiki. Druk 3D sprawia, że tytanowe tłumiki są jeszcze bardziej trwałe i lżejsze, co zwiększa ich atrakcyjność na rynku.