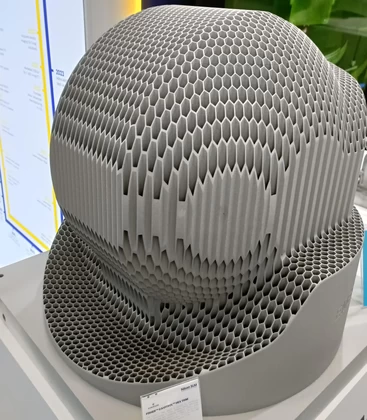
Emerson, globalna korporacja specjalizująca się w automatyce, monitoringu i sterowaniu dla szerokiego grona klientów przemysłowych, we współpracy z Nikon SLM Solutions wdrożyła nowatorskie podejście do produkcji zaawansowanych elementów zaworów kontrolnych. Dzięki wykorzystaniu technologii Selective Laser Melting (SLM) możliwe stało się stworzenie jednolitego komponentu dla urządzenia Fisher™ Cavitrol™ Hex trim, co wyeliminowało konieczność spawania wielu części i znacząco usprawniło proces produkcji.
Tradycyjna produkcja dużych elementów, takich jak NPS24 Cavitrol Hex trim, wymagała użycia mniejszych drukarek 3D do metalu, co skutkowało koniecznością składania i spawania poszczególnych części. Było to procesem czasochłonnym, kosztownym i niosącym ryzyko obniżenia jakości produktu. Współpraca z Nikon SLM Solutions umożliwiła zastosowanie zaawansowanej technologii druku 3D z metalu, pozwalając na produkcję całego komponentu w jednym procesie. Technologia SLM otworzyła nowe możliwości projektowe, takie jak tworzenie nietypowych kanałów przepływu, które zwiększyły wydajność urządzenia.
Fisher™ Cavitrol™ Hex Trim to zaawansowany element stosowany w zaworach obrotowych, zaprojektowany w celu redukcji lub eliminacji kawitacji w aplikacjach o wysokim obciążeniu. Kawitacja, czyli powstawanie i zapadanie się pęcherzyków pary w cieczy, może prowadzić do nadmiernych wibracji, uszkodzeń rurociągu za zaworem oraz pogorszenia kontroli przepływu. Cavitrol Hex Trim, dzięki swojej unikalnej konstrukcji z sześciokątnymi kanałami, separuje strumień cieczy, kondycjonuje jego przepływ i skutecznie minimalizuje hałas oraz wibracje spowodowane kawitacją. Dzięki temu zwiększa wydajność zaworu i przedłuża jego żywotność, jednocześnie poprawiając bezpieczeństwo i niezawodność całego systemu. Przy okazji jest to ulubiona część wystawiana na targach, jako demonstrator możliwości dużych drukarek Nikon SLM Solutions Krzysztofa Bonczara.