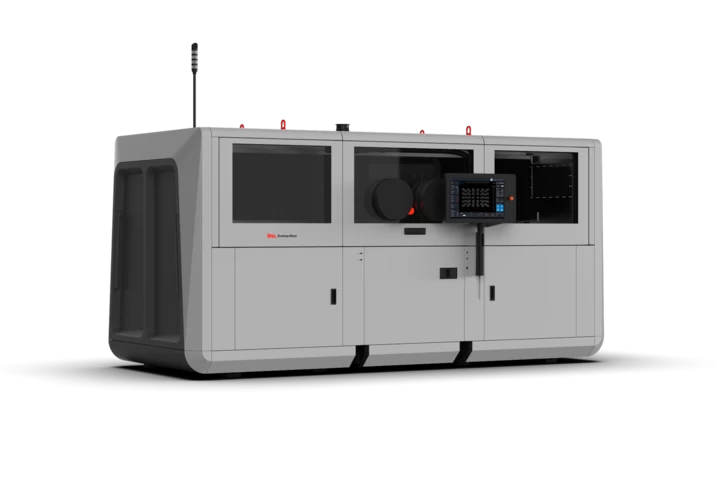
Seria drukarek z rodziny Production System™ to urządzenia, które wniosły nową jakość w postrzeganiu druku 3D z metalu przez pryzmat seryjnej produkcji części. Jednoprzebiegowy system Single Pass Jetting™ gwarantuje dużą wydajność, co w połączeniu z możliwą do osiągnięcia wysoką gęstością drukowanych części, ich powtarzalności i niskich kosztów produkcji jest rozwiązaniem wyjątkowym na rynku drukarek 3D do metalu. Dzięki otwartej platformie materiałowej możliwe jest korzystanie z szerokiej gamy dostępnych proszków metalowych różnych dostawców a fakt, iż urządzenia pracują w zamkniętym środowisku pracy, poszerza listę dostępnych do druku materiałów o metale reaktywne.